TYPES OF LOFT INSULATION.

1. SPRAY FOAM INSULATION
Spray Foam Insulation is a superior product when it comes to loft insulation. When sprayed at rafter level, it seals the home creating an air-tight warm roof structure which contributes to keeping your home warm in winter, cool in summer whilst lowering heating and cooling costs by up to 50%, which can’t be achieved with traditional insulation!
Spray foam insulation once applied, expands to roughly 100 times its original volume and as a result fills every crack and crevice to eliminate air leakage or infiltration.
To be honest spray foam loft insulation costs considerably more than traditional insulation, but it is the most superior form of insulation on the market today. I’m sure you would agree that the cheapest solutions can end up being your most expensive mistakes.
As well as insulating the roof, we do recommend the gables to be included to maximise efficiency.
PROS :
1.Eco Friendly: Spray foam insulation is an ecofriendly product and reduces your carbon footprint.
2.100% Water Blown: Icynene foam insulation Spray is 100% water blown with no harmful
chemical blowing agents.
3.Breathable insulation: Icynene open cell insulation allows the timbers to breathe,which
also prevents moulding and condensation.
5.Reduces Noise Pollution: Icynene Spray foam insulation minimises airborne sounds.
6.Fills all gaps: Spray foam insulation is ideal for roofs, walls, lofts, underfloor and attics.
7.Energy Saving: Helps in saving up to* 50% on your energy bills.
CONS:
1.Not a DIY product: Icynene Spray foam insulation can only be installed by a licensed accredited installer,
you cannot do it from a local store.
2.Not the cheapest Solution:Not the cheapest Solution: Spray foam insulation costs more than traditional insulation methods on the market.Spray foam is not the cheapest insulation solution, but it’s the most superior form of insulation on the market today.

2. FIBREGLASS INSULATION (TRADITIONAL)
The transfer of heat is slowed down with fiberglass insulation because the glass fibers trap air bubbles. These bubbles create an insulating effect by slowing heat exchange between areas and surfaces.
Fiberglass insulation usually comes in batts or rolls. In order to be completely effective, fiberglass insulation must be cut carefully around obstacles such as power sockets. This can be incredibly time consuming.
Fiberglass insulation is significantly cheaper than spray foam insulation, but it is also less effective, especially in winter. Fiberglass is the most common type of loft insulation, however, is outdated and has to be topped up every 5 years because it deteriorates through condensation issues.
Warning: The tiny fibers of glass from fiberglass insulation can irritate your skin and eyes. If you experience too much contact with fiberglass, it can cause what’s called irritant contact dermatitis, or inflammation of the skin. Breathing in fibers can also increase the difficulty of breathing.
Professional installation is required for spray foam insulation, where as fiberglass insulation can often be installed by homeowners themselves.
PROS:
1.Fibreglass insulation does not burn
2.Fibreglass insulation is available in High and Medium density options
3.Fibreglass insulation is inexpensive
4.Fibreglass or Glasswool insulation forms a protective vapour barrier.
CONS:
1.Fibreglass insulation starts SAGGING as time passes
2.Causes Skin irritation: The installers must wear protective wear when installing fibreglass to protect themselves from the “silver” released from Fibreglass.These silvers if inhaled will lead to skin and respiratory disease.
3.Harmful chemicals: Glasswool contains harmful chemicals like Formaldehyde which is
highly toxic.

3. CELLULOSE
Cellulose insulation includes cellulose cells that have natural insulating power. It is made of shredded paper plus a fire retardant chemical known as a borate. The paper is broken down into cellular fibers that provide insulation.
Cellulose insulation in installed into your loft using an insulation blower. The fibers flow through a long hose and are blown / sprayed into your loft space.The blown cellulose is prone to create dust that is blown into the holes or inadequate seals around fixtures. This is a health hazard.
Cellulose is more energy efficient than fiberglass insulation and does have better sound insulation but is still incomparable to spray foam insulation.
Both cellulose insulation and fiberglass insulation are low cost and have a similar price per squarer meter. However, as cellulose insulation often requires professional installation and specialised skills, it usually turns out to be more expensive.
PROS:
1.Ecofriendly product: Cellulose insulation is made from newspapers and therefore it is ecofriendly
2.Not an Expensive product: Cellulose insulation is the cheapest of all the insulation methods.
3.Energy Efficient: Cellulose is more energy efficient than fiberglass insulation.
CONS:
1.Moulding and Rotting: The efficiency of Cellulose decreases due to the insulation absorbing moisture and this causes moulding and rotting.
2.Sagging: Loose fill(Cellulose) saggs as time passes and this results in the decrease of performance.
3.Health Hazard: The blown cellulose is prone to create dust that is blown into the holes or inadequate
seals around fixtures.
WHY REMOVE YOUR INSUALTION ?
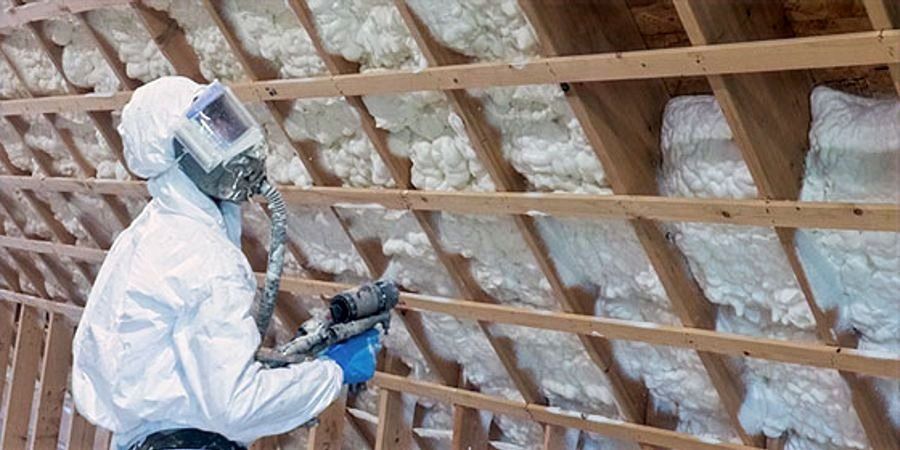
WHY REMOVE SPRAY FOAM INSULATION ?
Roof foam insulation has its positives. It’s versatile, flexible and can even help to support a building’s structure (in the case of closed cell spray foam).
However, it’s not all sunshine and roses. Here are some of the reasons you might be looking to get your spray foam removed:
Many surveyors will down-value properties that have this kind of insulation.
Some lenders won’t give you a mortgage on a property with spray foam insulation applied to the loft or roof.
Spray foam insulation can contribute towards condensation and damp, which can, in turn, cause your roof timbers to decay.
It can be messy and hard to decorate over.
Spray foam shouldn’t be used on listed properties.
It can make it hard to carry out roof repairs, such as fixing broken tiles or roof leaks.
If it’s not applied well, it could risk damaging the structure of your home. It could be covering up other damage.
/

WHY REMOVE FIBREGLASS INSULATION (TRADITIONAL) ?
Some people want to remove their fibre glass insulation, either because they are allergic or because they don’t want to breathe in the fibres when they are using the loft. There are clear reasons why you would want your insulation removed. The effects of coming into contact with fibreglass insulation include:
Irritation to eyes, nose and throat
Rash and itchiness
Stomach irritation if fibers are swallowed
Worsening of asthma and bronchitis
Also, if you have old paper based loose fill insulation, it may be a fire hazard, and as such you may want to look at getting it removed and updated.

WHY REMOVE YOUR CAVITY WALL INSULATION ?
In the 1980s, building regulations stipulated that insulation should be installed during the construction of new buildings. As soon as these regulations came into play, it became clear there were a huge number of slightly older properties that could also benefit from this type of insulation; however the only way to get the insulation into the cavity once the property was built was to inject it. Since the materials were cheap and the installation process was relatively simple, the Government really pushed the measure. Thousands of small installer companies popped up, knowing they could install the insulation in people’s homes and be well paid for the work.
As a result, any property with an unfilled cavity was targeted, regardless whether it was suitable or not – so obviously issues occurred. Some of these issues are laid out below:
The insulation material used was unsuitable – e.g. urea-formaldehyde. The problems with this insulating product were two-fold: Firstly, it breaks down, releasing (carcinogenic) formaldehyde into the home. Secondly, when the insulation breaks down it falls down the cavity, meaning walls higher up no longer benefit from the insulation.
When cavity walls were first introduced in the 1930s, the cavity’s sole purpose was to prevent water crossing the wall from outside to inside, causing damp in the home. As a result the early cavities were very thin – insulation could cause bridges between the two skins of brick, allowing water to cross and leading to damp issues in the home.
The insulation was installed incorrectly. When the cavity wall installer puts the cavity wall insulation in the gap between the two skins of brick, the wall needs to be drilled in various places to allow an even distribution of the insulation. If the distances between the drilled holes were incorrect, then the insulation would not meet leading to cold spots.
Another issue was corner-cutting. Since installers are paid per m2 of wall, they need to do the jobs as quick as possible. When beads are injected into the cavity wall they are injected with a uPVC glue which binds all the beads together. The problem is that doing this properly – injecting the glue with the beads – takes about 3 times longer than installing the beads alone. Some installers wouldn’t bother, as they were looking to maximise profits by doing multiple jobs in the same day. This often led to beads ‘settling’ in the bottom of the cavity, meaning there was no real insulating impact on the upper parts of the wall.
Until the development of new technology, cavity wall insulation wasn’t suitable for every property. If a wall is privy to driving rain for instance, the cavity is required to prevent ingress of water into the home. If these walls were retrofitted with old-fashioned types of cavity wall insulation, it could quickly lead to damp issues – this is most prevalent in coastal regions.
Another example of a wall being unsuitable is when we hear of timber frame properties having had cavity wall insulation installed. These properties should never have cavity wall insulation installed. However an untrained or untrustworthy installer may have installed anyway to make sure they get paid for the job. We get several phone calls a month from homes who are in this situation and are trying to sell their properties, but are finding it impossible since mortgage companies won’t allow prospective buyers to get a mortgage on the property until the cavity wall insulation is removed.
The final reason is when someone has just bought a property previously installed with cavity wall insulation. In some cases, the insulation causes allergies for the new homeowner and again this needs to be removed despite the energy savings resulting from the installed cavity wall insulation.